Những công nghệ thiết kế chế tạo khuôn cần biết ( khuôn nhựa, khuôn đúc)
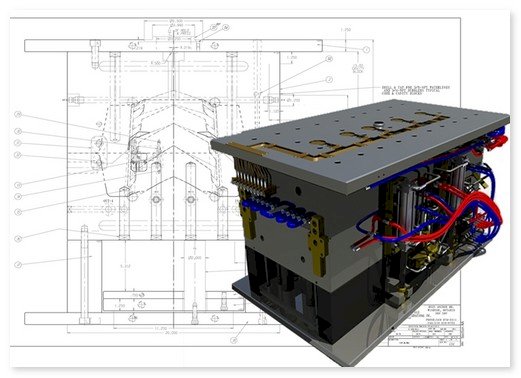
Công nghệ ép phun.
Công nghệ ép phun là công nghệ đẩy, ép nguyên liệu nóng chảy vào một hệ thống tạo hình dáng có sẵn được gọi là hệ thống khuôn, sau đó làm nguội để nguyên liệu lỏng kết tinh và đưa sản phẩm ra ngoài. Một quá trình tuần hoàn như vậy gọi là một chu kỳ ép phun. Chu kỳ càng ngắn thì giá thành sản phẩm càng giảm. Do đó, trong lĩnh vực ép phun người ta thường tính giá thành dựa trên chu kỳ của một lần ép phun.
Khuôn mẫu là gì?
Khuôn hay còn gọi là khuôn mẫu chính là trung tâm của công nghệ ép phun. Khuôn được gia công tạo hình dựa trên hình dạng sản phẩm mong muốn. Sản phẩm ép phun được định hình dạng nhờ vào cấu tạo và hình dạng của lòng khuôn (hay còn gọi là lõi khuôn, cuốc khuôn…).
Khuôn gồm 2 bộ phận chính được gọi là khuôn đực và khuôn cái. Trong ngôn ngữ kỹ thuật và các nhà máy công nghiệp chế tạo khuôn. Người ta chia khuôn thành 2 phần; phần cố định khuôn và phần di động khuôn.
Phần cố định ( khuôn cái) là phần đứng yên trong cả quá trình ép phun. Phần này được kết nối với vòi phun của máy ép để phun nhựa vào lòng khuôn. Phần này bao gồm lõi bên phần cố định, trục dẫn hướng, vòi rót nhựa, tấm khuôn cố định…
Phần di động (khuôn đực); Là phần sẽ di chuyển khi đóng khuôn hoặc mở khuôn trong một chu kỳ ép phun. Phần này có tác dụng mở khuôn ra để lấy sản phẩm và runner ra ngoài sau đó ép sát khuôn lại để nguyên liệu không bị xì ra (tạo ba vớ) bởi áp lực trong suốt quá trình phun.
Ngoài 2 phần chính cấu tạo nên khuôn, một số khuôn phức tạp còn có thêm phần bệ trượt, hệ thống motor (khuôn tạo ren), hệ thống thủy lực…
Cấu tạo chung của khuôn ép nhựa mà bạn cần phải biết
Sơ đồ phân rã của một bộ khuôn
Tấm kẹp trước: Chức năng chính để kẹp chắc khuôn cái vào máy ép nhựa (2 phần vai dư ra dùng để kẹp chặt vào máy ép nhựa)
Vỏ Khuôn cái: Chức năng chính để gắn Khuôn cái
Vỏ Khuôn đực: Chức năng chính để gắn khuôn đực
Gối Đở: Chức năng chính để tạo khoảng không gian trống cho tấm đẩy và ty lói di chuyển.
Tấm giữ: Chức năng chính để giữ các ty lói không rơi ra khỏi tấm đẩy
Khuôn cái: Chức năng chính để tạo hình cho sản phẩm
Khuôn Dương: Chức năng chính để tạo hình cho sản phẩm
Vòng Định Vị: Dùng để định vị Khuôn cái với máy ép nhựa
Bạc cuống phun: Dẫn nhựa từ đầu phun của máy ép vào kênh dẫn nhựa
Chốt định vị: Định vị giữa khuôn cái và khuôn đực ( Giữ chặt khuôn cái và đực khi nhựa bơm vào lòng khuôn)
Chốt dẫn hướng & Bạc dẫn hướng: Dẫn hướng cho khuôn âm và khuôn dương khi đóng khuôn
Dẫn hướng lói: Cũng gồm chốt dẫn hướng lói và bạc dẫn hướng lói. Dùng để dẫn hướng cho tấm đẩy và ty lói khi di chuyển
Chốt hồi & Lò xo hồi: Dùng để đẩy tấm giữ và tấm đẩy về khi đóng khuôn
Gối đở phụ: Đở khuôn dương (Phụ cho gối đở)
Ty Lói: Để đẩy sản phẩm ra khỏi khuôn
Lói keo: Dùng để đẫy đường keo ra khỏi khuôn
Quy trình lắp ráp 1 bộ khuôn
Bước 1: Nhập tấm khuôn vào mô hình. Bước 2: Lắp bạc dẫn hướng vào tấm khuôn trên.
Bước 3:Lắp tấm kẹp với khuôn trên.
Bước 4:Lắp bạc cuống phun vào tấm kẹp trên và lắp bu lông để dữ hai tấm khuôn với nhau.
Bước 5: Lắp vòng định vị với tấm kẹp trên và hai bu lông giữ vòng đinh vị.
Bước 6:Lắp chốt dẫn hướng vào tấm khuôn dưới.
Bước 7:Lắp tấm đẩy vào (nếu dùng ty đẩy thì lắp ty đẩy vào tấm giữ cùng lúc khi lắp chốt hồi.
Bước 8:Lắp bốn lò xo và hai gối đỡ.
Bước 9: Lắp tấm giữ và bốn chốt hồi.
Bước 10:Lắp tấm đẩy và bốn bu lông liên kết tấm đẩy và tấm giữ.
Bước 11:Lắp tấm kẹp trên và bốn bu lông liên kết phần di động.
Quy trình khuôn thổi ép chai nhựa
Phần này sẽ giới thiệu về quy trình chung nhất, còn máy ép khuôn thổi có nhiều loại, tùy theo năng suất và chi phí mà người ta có thể dùng hệ thống băng chuyền hoặc hệ thống khuôn quay, bạn có thể xem hình minh họa cho hai hệ thống máy ép khuôn thổi ở dưới.
Hình 1: Hệ thống dùng băng chuyền
Hình 2: Hệ thống quay
Nguyên lý tạo khuôn thổi cũng tương đối đơn giản, bạn sẽ có một phôi vật liệu nhựa nhiệt được gia nhiệt trước và đưa vào lòng khuôn, sau đó hệ thống sẽ bơm khí vào bên trong, vật liệu giản nở và bám vào thành khuôn tạo nên hình dạng của chai lọ mà bạn thiết kế.
Hình 3: QUy trình ép khuôn thổi
Giải thích một số thuật ngữ:
Extruder: máy nghiền ,cụm đùn
Air hose: Ống dẫn khí
Cooling line: Đường làm mát
Die Head: Đầu khuôn thổi
Blow Pin: Chốt thổi
Parision: Phôi thổi
Mold Half: Nửa khuôn
Molten Plastic: Keo, nhựa nóng chảy
Molded Part: Sản phẩm thổi
Phần thiết kế khuôn thì tương đối rườm rà, nếu chưa học kỹ thuật thì bạn sẽ cần ít nhất một năm để có thể làm chủ công nghệ này, vì phần thiết kế khuôn liên quan tới phần mềm, các thông số công nghệ khuôn, và gia công khuôn.
Phần thiết kế khuôn bạn có thể dùng phần mềm thông dụng như solidworks, còn gia công thì dùng phần mềm mastercam, Visi, Powermill, và bạn cũng có thể dùng phần mềm thiết kế và gia công khuôn hoàn chỉnh như Proe, NX, Catia, và phần mềm nào thì tùy thuộc vào công ty của bạn.
Hình 4: Cấu tạo cơ bản của bộ phận ép khuôn thổi
Trong kỹ thuật, cần nhiều bước để có thể cho ra sản phẩm cuối cùng, vì vậy bạn cũng nên hiểu một số công đoạn khác để việc làm việc nhóm được hiệu quả nhất.
Hình 5: Quá trình hình thành và thay đổi của phôi thành sản phẩm.
Bạn có thể tham khảo video hoàn thiện về khuôn thổi để nắm hết các vấn đề mà bạn quan tâm.
Linkdown:
https://www.mediafire.com/?41jkh6v7l98d3yg
Video khuôn thổi:
Kỹ thuật đúc nhôm
Nhắc đến hợp kim nhôm chắc hẳn ai cũng biết đến nó, hợp kim nhôm được sử dụng làm ra rất nhiều sản phẩm với mẫu mã đẹp có những sản phẩm mà chúng ta sử dụng trong đời sống hằng ngày.Vậy làm thể nào để có được các sản phẩm đó?Phải qua các công công đoạn gia công đúc vật liệu.
Hợp kim nhôm là một trong các kim loại có thể đúc được bằng nhiều phương pháp như đúc áp lực, đúc khuôn kim loại, đúc khuôn cát , khuôn thạch cao, đúc mẫu chảy, đúc liên tục và cũng có thể áp dụng trong đúc mẫu chảy.
Ngày nay để chế tạo ra các chi tiết máy người thường sử dụng hợp kim nhôm bởi nhờ vào các yếu tố như giá thành rẻ, có tính khả thi cao và đem lại chất lượng tốt.
Chúng ta có thể đúc hợp kim nhôm bằng nhiều cách:
-Đúc khuôn kim loại
Đúc khuôn kim loại cho ta sản phẩm có cơ tính rất cao, vật đúc hoàn hảo hơn, nhưng cũng được áp dụng với những kim loại có độ chảy loãng cao và có khả năng chống nứt nóng.
Một số loại hợp kim nhôm hay được sử dụng trong đúc khuôn kim loại:
+ 366: chế tạo pistong oto
+ 355.0, C355.0, A357.0: hộp số, hang không, một số bộ phận của tên lửa (các chi tiết yêu cầu độ bền cao)
+ 356.0, A356.0 Các chi tiết trong máy dụng cụ, bánh xe máy bay, bộ phận trong máy bơm…
-Đúc khuôn cát
Đúc khuôn cát chúng ta có thể đúc các chi tiết lớn, phức tạp hơn do có thể làm ruột.
-Đúc mẫu cháy
-Đúc khuôn vỏ mỏng
Khuôn dập nguội
Ngày nay với sự phát triển của nền kinh tế, các ngành công nghiệp ô tô,các đồ dùng gia dụng, ngành công nghiệp phụ trợ….phát triển ngày càng cao cần có một số lượng lớn khuôn dập nguội như khuôn đột dập,khuôn dập vuốt, dập sâu..Khuôn dập nguội là sản phẩm biến dạng vật liệu dưới tác dụng của áp lực tạo hình ở trạng thái nguội. Sản phẩm của khuôn dập nguội rất đa dạng như chậu rửa mặt, nồi, chảo, đồ dùng y tế,bình xăng, ống bô xe máy…
Khuôn dập được sử dụng rất đa dạng với các loiaj khác nhau,dựa vào tính năng có thể chia ra làm 2 loại chính đó là khuôn dập vuốt,sâu và khuôn đột dập.
Cấu tạo của khuôn gồm hai phần: chày và cối. Chày được gắn với búa, chuyến động nhờ áp lực của búa, cối là bộ phận cố định.
Các yêu cầu của khuôn dập nguội:
+ Cần có tính chống mòn cao
+ Đảm bảo được độ cứng và độ dai nhất định
Yêu cầu các loại thép để làm khuôn dập nguội là: các loại thép làm khuôn dập nguội phải có thành phần cacbon cao (xấp xỉ 1%), nếu khuôn chịu va đập nhiều thì dùng loại có lượng cacbon thấp hơn (0,4 – 0,6%)
Quy trình làm khuôn cát
Quy trình làm khuôn cát thì bao gồm 6 bước
Bước 1: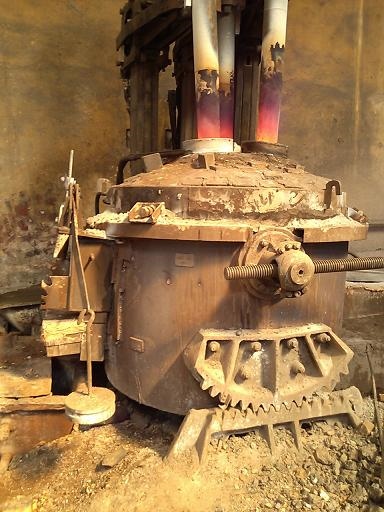
Chuẩn bị
Hỗn hợp làm khuôn
+Cát áo, cát đệm
+ Cát đệm
Thành phần
Cát 60%
Pentonic 24%
Nước thủy tinh 8%
Chất độn 5%
Nước 3%
Chọn mặt phân khuôn tối ưu
Bước 2:
Làm khuôn dưới
-Đặt mẫu lên tấm ván mẫu sao cho mặt phân khuôn đã chọn tiếp xúc với tấm ván mẫu
-Bố trí lòng khuôn
-Cho cát đệm vào điền đầy khuôn
– Dùng chày giã khuôn chặt đều
+ Tạo độ bền cơ học cho khuôn
+ In hình mẫu rõ ràng hơn
– Gạt phẳng cát dư phía trên
– Xiên lõi để không khí thoát ra lỗ này cách lỗ kia khoảng 40 mm,
-Lật khuôn 1800
Bước 3 :
Làm khuôn trên
-Phân khuôn
-Lắp khuôn trên vào khuôn dưới theo đúng chốt định vị
-Lắp chốt định vị
-Bố trí ống rót
-Cho hỗn hợp cát áo vào che kín mẫu
-Gỡ khuôn, gạt cát dư, xiên hơi
– Cắt phễu rót
Bước 4:
Lấy mẫu sửa khuôn
Nhấc hòm khuôn theo phương thẳng đứng lên trên quay 180°
Cắt rãnh lọc xỉ đi qua chân ống rót
Lấy dụng cụ làm khuôn miết nhẵn phần tiếp xúc với mẫu
Rãnh dẫn kim loại nằm dưới rãnh lọc xỉ có diện tích hình thang
Đóng đinh mẫu
Đánh long mẫu để dễ rút
Rút thẳng lên trên để dễ rút
Rút thẳng lên trên theo phương thẳng đứng để lại trong lòng khuôn không gian rỗng
Lấy mẫu xong sẽ xới khuôn
Bước 5:
Làm lõi
Lau sạch và ghép 2 nửa hộp lõi lại với nhau sau đó đạt lên sau đó đạt lên tấm
Cho hỗn hợp lõi vào
Lấy cây sắt đánh vào mẫu, nhấc lên
Sơn lõi ( chống khả năng cháy cát, làm bóng)
Sấy khô lõi
Bước 6:
Lắp lỗi và ráp khuôn
Kiểm tra lõi, khuôn trên, khuôn dưới
Lắp lõi, ráp khuôn
Tính trọng lượng gang đè khuôn
Kỹ thuật đúc khuôn mẫu chảy
- Đúc mẫu chảy
Đúc mẫu chảy là một phương pháp đúc tiên tiến được phát minh bởi ông H.F.Shroyer người Mỹ, vào năm 1958 và được nhận bằng phát minh, theo đúng tên gọi của nó, là làm cho mẫu bằng sáp chảy lỏng ra như một chất lỏng và thoát khỏi khuôn. Mẫu chảy thoát ra khỏi khuôn và để lại một hốc khuôn có hình dáng tương tự như hình dáng vật đúc. Rót kim loại lỏng vào khuôn, kim loại đông đặc và tạo thành vật đúc.
- Yêu cầu của sáp:
- Đảm bảo sao cho nhiệt độ chảy thấp (khoảng 55 – 900C)
- Mẫu bền, co giãn ít, ổn định kích thước dưới nhiệt độ thường.
- Tạo độ bám huyền phù tốt.
- Những chi tiết thường đúc mẫu chảy:
Những chi tiết đúc phức tạp, hay trong sản xuất hàng loạt để chế tạo các dụng cụ như dao phay, dao chuốt; chế tạo các loại bánh răng; líp xe đạp; đĩa moto; các phụ tùng trong máy nổ… vật đúc có khối lượng từ 0,02 ÷ 100kg; chiều dày đến 0,3mm và đường kính lỗ đến 2mm.
- Lớp vỏ huyền phù
Huyền phù là hỗn hợp của thạch cao (chất kết dính) và bột cát thạch anh (chất chịu lửa) nếu đúc hợp kim có nhiệt độ nóng chảy thấp. Nếu đúc hợp kim có nhiệt độ nóng chảy cao, hỗn hợp huyền phù gồm sillimanite hoặc bột zircon (chất chịu lửa) và silica (chất kết dính). Tùy vào mức độ nhẵn của hốc khuôn mà thêm vào sillimanite và ethyl silicate cho phù hợp. Thành phần của huyền phù thay đổi từ lớp vỏ trong ra ngoài. Khuôn có thể được dùng trực tiếp để đúc những chi tiết nhẹ (đúc vỏ mỏng) hoặc được đặt vào khuôn lớn, bao phủ bằng cát để đúc những chi tiết lớn hơn (đúc khuôn cát).
Hỗn hợp làm huyền phù:
+ 1kg : nước thủy tinh
+ 400g : bột thạch anh ( vật liệu chịu lửa)
+ 100g :bentonite (tăng khả năng chịu lửa và kết dính )
Trước khi rót kim loại vào, khuôn cần được nung lên 900 – 1000ºC để loại bỏ hết sáp dư, làm cứng chất kết dính. Ngoài ra, nung khuôn còn giúp kim loại lỏng điền đầy khuôn hoàn toàn.
- Phương pháp này có ưu nhược điểm so với đúc trong khuôn cát như sau:
Ưu điểm:
-Đúc trong khuôn mẫu chảy là một phương pháp mới nhiều ưu điểm. So với đúc bằng khuôn cát, đúc mẫu chảy có thể làm được các chi tiết phức tạp, có thành mỏng, chất lượng bề mặt cao, giảm đáng kể lượng gia công cơ khí, nhiều chi tiết đúc xong có thể sử dụng ngay. Đúc mẫu chảy có thể làm được các sản phẩm có trọng lượng từ vài gram đến vài chục kilogram.
-Đúc được những hợp kim khó chảy như thép không rỉ, thép gió…
-Độ chính xác và độ bóng bề mặt vật đúc rất cao vì: độ chính xác của mẫu chảy lớn, không có mặt phân khuôn nên không có sự sai lệch khuôn và khuyết tật do lắp ráp khuôn gây ra, không có nguyên công rút mẫu nên giảm được sai số do việc rút mẫu, giảm đáng kể lượng dư gia công cơ khí, rót kim loại lỏng vào khuôn đã được nung nóng nên giảm ứng suất nhiệt do đó vật đúc ít bị nứt, cong vênh.
-Giảm thời gian gia công cơ khí
Nhược điểm:
- Cường độ lao động cao
- Chu trình sản xuất dài,
- Giá thành chế tạo khuôn cao.
- Khuôn chỉ đúc được một lần